Industrial Heat Exchangers: Your Buyer’s Guide to Types, Materials, and Smart Sourcing
Heat exchangers are essential components in virtually every industrial process that involves heating, cooling, or temperature maintenance. From power plants and chemical refineries to food processing and HVAC systems, these devices facilitate the efficient transfer of thermal energy between fluids. However, for purchasers, navigating the vast array of heat exchanger types, materials, and suppliers can be complex, with the choice significantly impacting performance, lifespan, and ultimately, the total cost of ownership (TCO).
Understanding the fundamental types and materials, along with smart sourcing strategies, is key to making an informed purchase decision that delivers optimal value. This guide provides an overview for buyers looking to acquire the right heat exchanger for their specific needs.
Main Types of Industrial Heat Exchangers
Industrial heat exchangers come in numerous configurations, each suited to different applications and operating conditions. The most common types include:
- Shell and Tube Heat Exchangers (STHX): The most widespread type, consisting of a shell containing a bundle of tubes. One fluid flows through the tubes, the other around them in the shell. They are known for their robustness, ability to handle high pressures and temperatures, and versatility across various fluids, including those with fouling potential on the shell side. Different internal configurations (like fixed tubesheet, U-tube, floating head) cater to thermal expansion and maintenance needs.
- Plate Heat Exchangers (PHE): These use a series of thin, corrugated plates to create channels for fluid flow. They offer high thermal efficiency and a compact footprint compared to STHXs for similar duties, and gasketed versions (GPHEs) provide easy access for inspection and cleaning. They are typically used in applications with moderate pressures and temperatures.
- Brazed Plate Heat Exchangers (BPHE): Similar to PHEs but permanently joined by brazing without gaskets. This allows them to operate at higher pressures and temperatures than GPHEs and makes them very compact and efficient. They are not openable for mechanical cleaning and are often used in HVAC, refrigeration, and smaller industrial applications.
- Air-Cooled Heat Exchangers (Fin-Fan Coolers): These transfer heat from a process fluid to ambient air, typically using finned tubes to maximize surface area, with fans to move the air. They are essential in locations where water is scarce or expensive as a cooling medium but require a larger footprint than liquid-cooled types.
- Double Pipe Heat Exchangers: A simple design where one pipe is concentrated within a larger pipe. Fluids flow in the inner pipe and the annular space between the pipes, usually in counter-current flow. They are suitable for small duties, high pressures, or handling fluids with high fouling potential on one side due to high velocities.
- Other types like Spiral Heat Exchangers (good for challenging fluids with high solids or viscosity), Plate-Fin Heat Exchangers (very compact, often for gas or cryogenic service), and Scraped Surface Heat Exchangers (for viscous or crystallizing fluids) are used in more specialized applications.
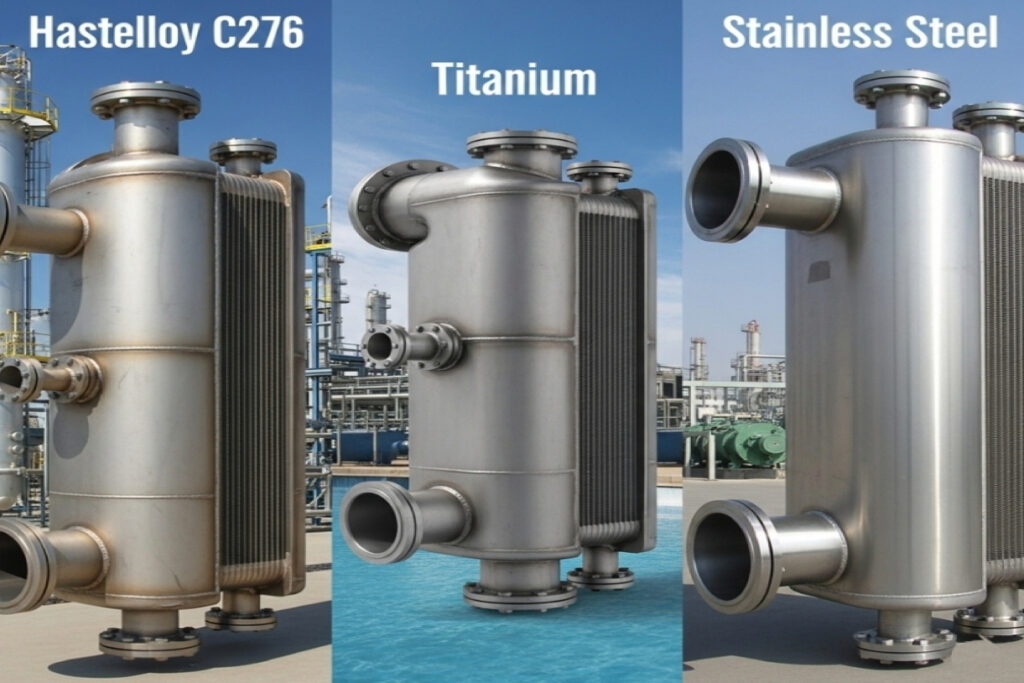
Choosing the Right Material(s): A Critical Decision
The materials used to construct heat exchangers are crucial for their performance, durability, and cost. Material selection depends heavily on the corrosiveness, temperature, pressure, and physical properties of the fluids involved, as well as cost and fabrication considerations. Common material categories include:
- Carbon Steel: An economical choice for shells and non-critical components when handling non-corrosive or mildly corrosive fluids at moderate temperatures and pressures (like steam, water in closed loops, non-corrosive hydrocarbons).
- Stainless Steels: A versatile family (including AISI 304, 316, Duplex, Super Austenitic like SMO 254) offering varying degrees of corrosion resistance, particularly against oxidation and some chemicals. Higher grades provide better resistance to chlorides and acids. Widely used for tubes and plates in various types of heat exchangers.
- Copper Alloys: Known for excellent thermal conductivity (e.g., Brass, Copper-Nickel). Often used for tubes or plates in water-to-water or steam-to-water heat exchangers, especially in HVAC and marine applications, but susceptible to attack by certain chemicals.
- Nickel Alloys: Offer broad and severe corrosion resistance beyond stainless steels (e.g., Alloy 400, Alloy 625, Hastelloy C-276). Used for tubes or plates in highly aggressive chemical environments involving reducing acids, complex media, or high temperatures where stainless steel fails.
- Titanium Alloys: Provide exceptional resistance to chlorides, seawater, and oxidizing acids. Essential for highly corrosive marine, desalination, and chemical processing applications where even high-grade stainless steels or some nickel alloys would pit or crack.
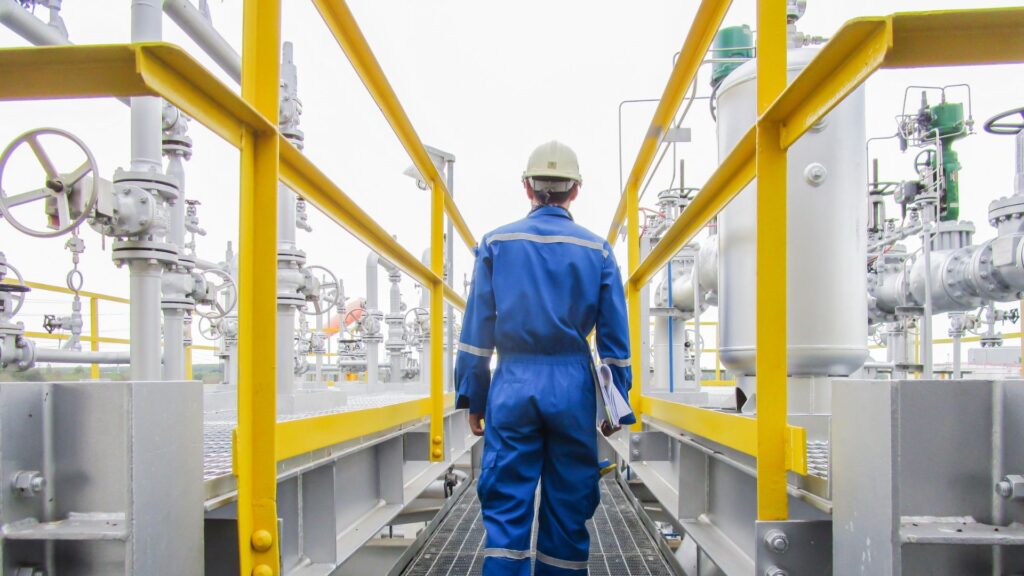
History and Evolution: From Ancient Ideas to Modern Design
The basic principle of heat exchange is ancient, seen in early heating systems and distillation. Industrial heat exchangers evolved significantly with the Industrial Revolution, driven by steam power and manufacturing needs. Simple coil-in-vessel designs gave way to more sophisticated shell and tube configurations in the late 19th and early 20th centuries, becoming the standard for high-pressure, high-temperature duties. Plate heat exchangers emerged in the 1920s as a more compact and efficient alternative, initially for the dairy industry. Later developments included brazed and welded plate designs, air-cooled types for water conservation, and highly compact designs like plate-fins for specialized uses. The development of new materials throughout the 20th century (stainless steels, nickel alloys, titanium) enabled heat exchangers to handle increasingly aggressive and extreme process conditions. The design principles are rooted in fundamental physics – thermodynamics for heat transfer rates and fluid dynamics for pressure drop and flow behavior.
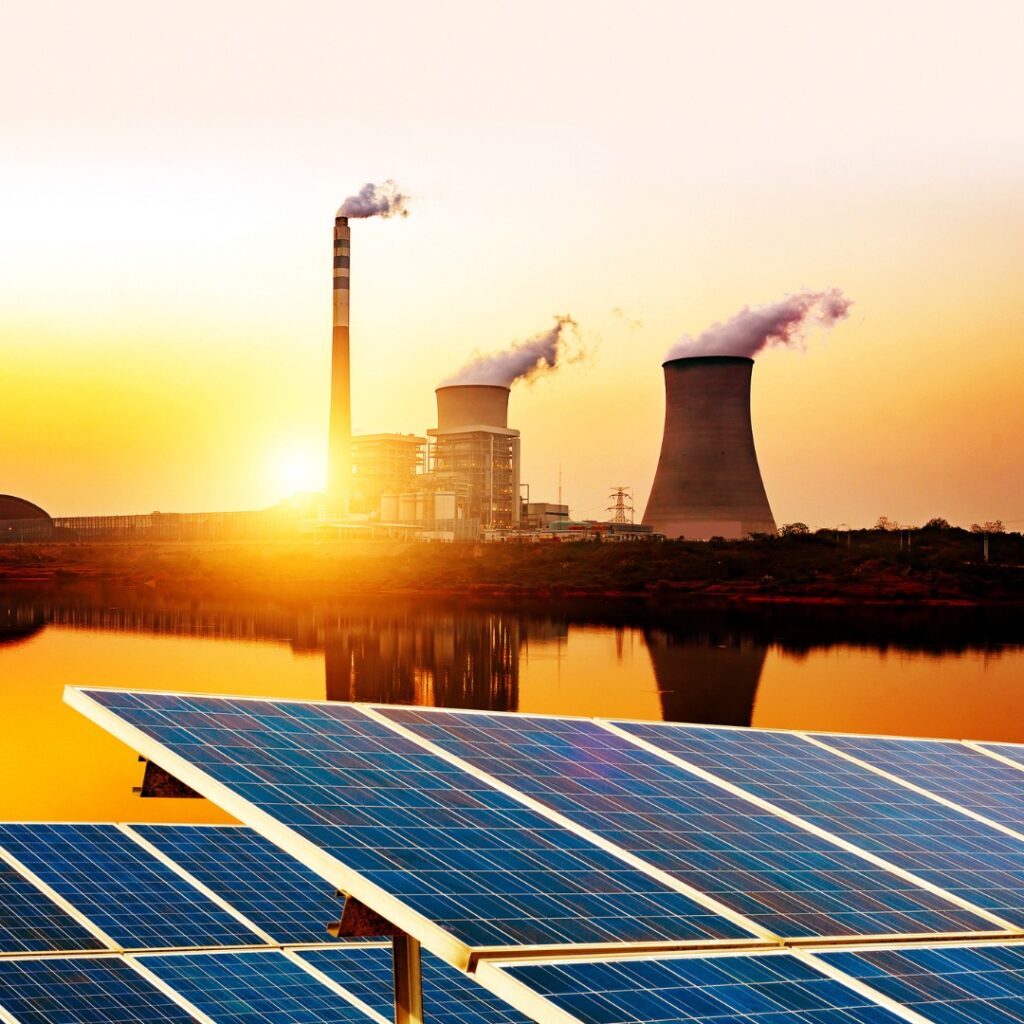
Global Supply Chain: Sources and Main Suppliers
The journey of a heat exchanger begins with raw materials mined from the earth: iron ore (for steel), nickel, chromium, molybdenum (for stainless and nickel alloys), titanium (from ilmenite/rutile), and copper. These are processed into mill products (plates, sheets, tubes) by global alloy producers.
- Raw Material Sources: Key mining regions worldwide (e.g., Nickel: Indonesia, Philippines, Russia; Titanium: Australia, South Africa; Molybdenum: China, USA).
- Alloy Producers: Major companies specialize in producing these metals and alloys (e.g., for nickel/Hastelloy: Haynes International, Special Metals, VDM Metals; for Titanium: Timet, VSMPO-AVISMA).
- Heat Exchanger Manufacturers (Suppliers): These companies design, fabricate, and supply the final heat exchanger units. They purchase mill products from alloy producers and process them (forming plates, welding tubes, assembling components) into finished exchangers. Major global manufacturers include Alfa Laval, GEA, Kelvion, Koch Heat Transfer, Chart Industries, Tranter, and many others worldwide. These suppliers vary in their specialization across different heat exchanger types and materials.
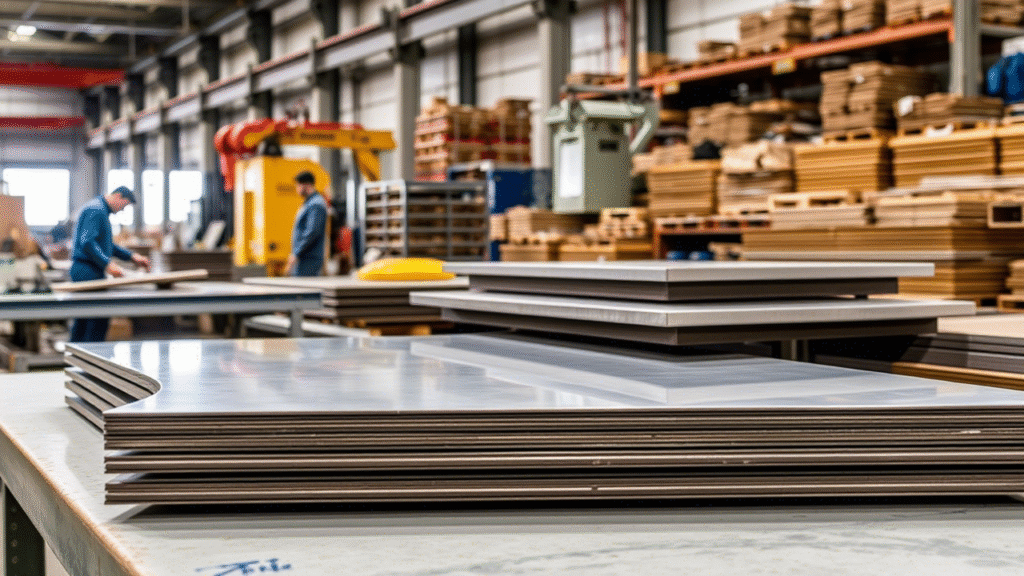
Sourcing Strategies: Getting the Best Price (Value) for Your Heat Exchanger
For purchasers, securing the right heat exchanger at a competitive price requires a strategic approach focused on value rather than just the lowest initial cost.
- Accurate Needs Assessment & Specification: This is the most critical step. Work with experienced engineers to define your process precisely: heat duty, temperatures, pressures, flow rates, full fluid compositions, and site environmental conditions. An accurate specification dictates the correct type and material needed. Any inaccuracy here leads to oversizing (wasted money) or undersizing/wrong material (failure, downtime, more expensive in the long run).
- Select the Right Type for the Application: Don’t default to the most common type. Evaluate if a compact PHE is a better fit than an STHX for a specific duty, or if an STHX is necessary for high pressure where a PHE isn’t suitable. The right type often provides the best balance of thermal performance, footprint, and maintainability for your needs.
- Optimize Material Selection Based on Corrosion Data: Avoid over-specifying expensive high alloys if a lower-cost stainless steel or a less exotic nickel alloy will suffice for the exact corrosive conditions (temperatures, concentrations, impurities matter greatly). Get expert metallurgical advice to match the material precisely to the environment.
- Focus on Total Cost of Ownership (TCO): The “best price” is the one that minimizes cost over the equipment’s entire lifespan, not just the purchase price. Factor in energy consumption (efficiency differences between types), maintenance frequency and cost (cleaning, gaskets, seals, spare parts), expected lifespan, and the significant cost of unplanned downtime if the unit fails prematurely due to incorrect selection or material.
- Evaluate Suppliers Beyond Price: Look for suppliers with a proven track record and expertise in the specific type and materials you need. Consider their engineering support, quality control, warranty, lead time, and after-sales service (availability of spare parts, technical support). A slightly higher initial price from a reliable, expert supplier can provide better long-term value.
- Standardization vs. Customization: Inquire if a standard or semi-standard model from a supplier can meet your needs. Fully custom designs are typically more expensive and have longer lead times.
- Consider Aftermarket Support: Availability and cost of spare parts (gaskets, plates, tubes, seals) vary by type, material, and supplier. This impacts maintenance costs over the life of the unit.
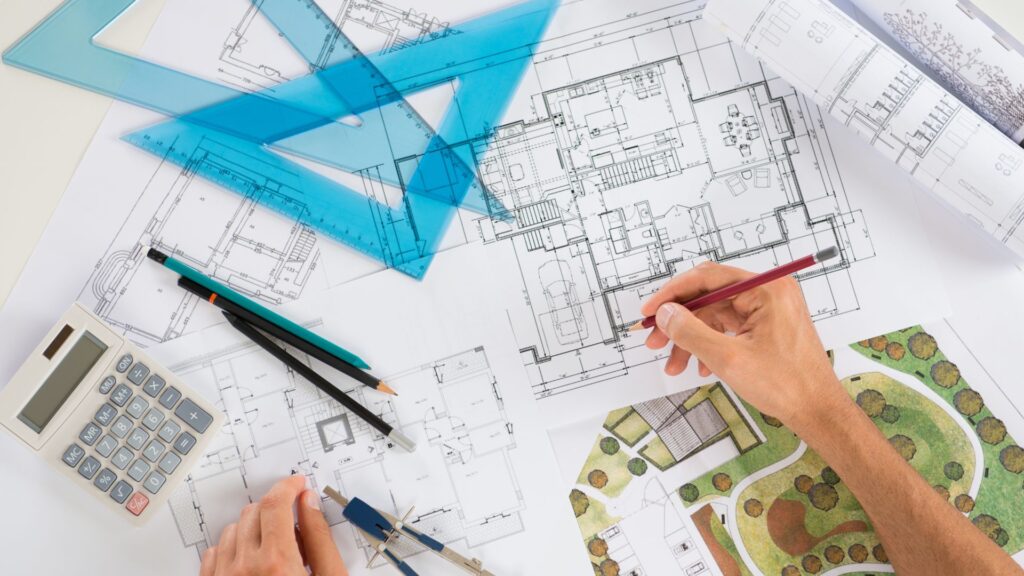
Conclusion
Industrial heat exchangers are diverse and complex pieces of equipment, with their type, materials, and design fundamentally impacting their performance and cost. From the ubiquitous Shell and Tube to the compact Plate designs, and materials ranging from Carbon Steel to exotic Titanium and Hastelloy, the right choice requires careful consideration of process conditions and operational needs. For purchasers, sourcing the “best price” means strategically evaluating options based on total cost of ownership, precise technical requirements, and the expertise of potential suppliers.
Navigating this complex landscape of types, materials, and suppliers demands significant knowledge. At HeatingFormula, we specialize in advanced heat transfer solutions and provide expert guidance to purchasers looking to select the most suitable and cost-effective heat exchanger for their specific industrial applications. We assist you in evaluating different types and materials based on your process needs, ensuring optimal performance and long-term value. Explore our GPHE Selection Guide for personalized expert consultation on choosing the right heat exchanger, material options, and sourcing reliable GPHE Spare Parts for your equipment.
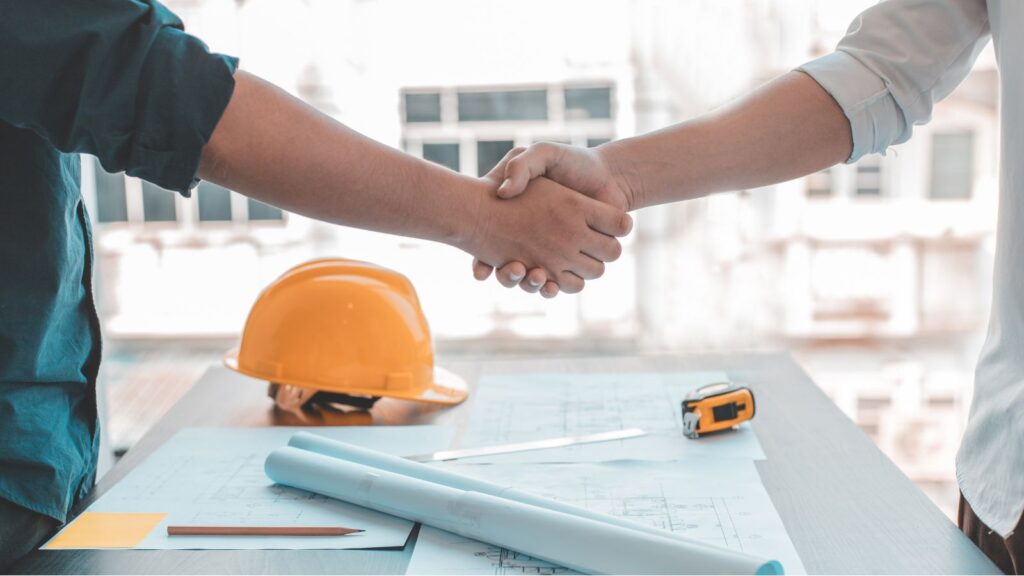
Frequently Asked Questions (FAQ) for Heat Exchanger Purchasers
What’s the most common type of industrial heat exchanger?
The Shell and Tube Heat Exchanger (STHX) is the most widely used type across industries due to its robustness and versatility.
What’s the most thermally efficient heat exchanger type per unit volume?
Plate Heat Exchangers (PHEs) generally offer very high thermal efficiency and compactness compared to other types for many applications.
What material is typically recommended for heat exchangers handling seawater?
Titanium alloys are usually the primary recommendation for handling seawater due to their exceptional resistance to chlorides, although specific conditions may allow for super austenitic stainless steels or certain copper-nickel alloys. Always consult an expert for your specific conditions.
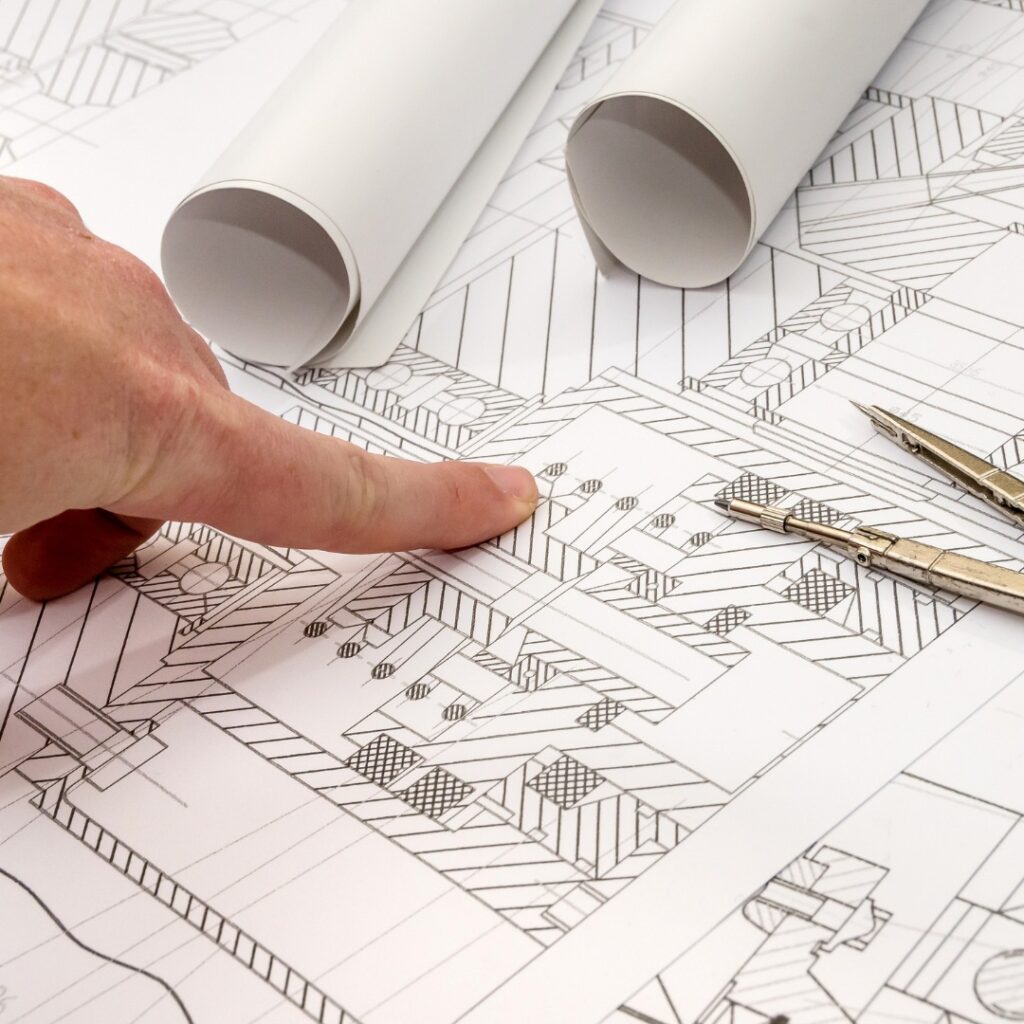
How do material choice and heat exchanger type affect the purchase price?
Both significantly impact the price. High-performance materials like Hastelloy or Titanium can increase the cost many times over stainless steel. The type affects complexity, size, and fabrication requirements, leading to different cost structures (e.g., a large custom STHX vs. a standard BPHE).
What does TCO mean in heat exchanger purchasing?
TCO stands for Total Cost of Ownership. For a heat exchanger, this includes not just the initial purchase price but also installation costs, ongoing energy consumption (due to efficiency and pressure drop), routine maintenance (cleaning, gasket replacement, spare parts), expected lifespan, and the potential costs of unplanned downtime or process inefficiency due to the heat exchanger.
Where can I get expert help choosing and sourcing the right heat exchanger?
Expert heat exchanger manufacturers and consultants can provide critical assistance. They help accurately assess your process needs, recommend the most suitable type and material, optimize the sizing, and provide reliable sourcing.