The Engineer’s Key to Efficiency: Understanding the Overall Heat Transfer Coefficient (U-Value) For Heat Exchanger
In the world of industrial processing, efficiency isn’t just a buzzword—it’s the critical factor that separates profitable operations from wasteful ones. At the heart of countless thermal processes, from pasteurizing milk to cooling a skyscraper, lies the heat exchanger. But how do we measure its performance? The answer is a crucial metric known as the Overall Heat Transfer Coefficient, or U-value.
Long before the first modern heat exchanger was built, scientists like Jean-Baptiste Joseph Fourier were laying the groundwork for our understanding of thermal dynamics in the early 19th century. Their pioneering work on heat conduction paved the way for engineers to eventually quantify and optimize thermal transfer. Today, the U-value stands as a direct legacy of this history—a single number that tells us how effectively a heat exchanger is doing its job.
What Exactly is the Overall Heat Transfer Coefficient (U-Value)?
In simple terms, the U-value is a measure of how well a heat exchanger can transfer thermal energy from a hot fluid to a colder one. Think of it as the total thermal conductance of the device. The higher the U-value, the more efficient the heat exchanger is at transferring heat with a given surface area and temperature difference.
For the technically inclined, the relationship is defined by the formula:
Q=U⋅A⋅ΔTlm
Where:
- Q is the rate of heat transfer (in Watts).
- U is the Overall Heat Transfer Coefficient (in W/(m2K) or W/(m2∘C)).
- A is the total heat transfer surface area (in m2).
- ΔTlm is the Logarithmic Mean Temperature Difference (LMTD), which represents the average temperature driving force between the two fluids.
A high U-value indicates superior performance, meaning you can achieve your desired temperature change using less surface area, resulting in a more compact and cost-effective unit.
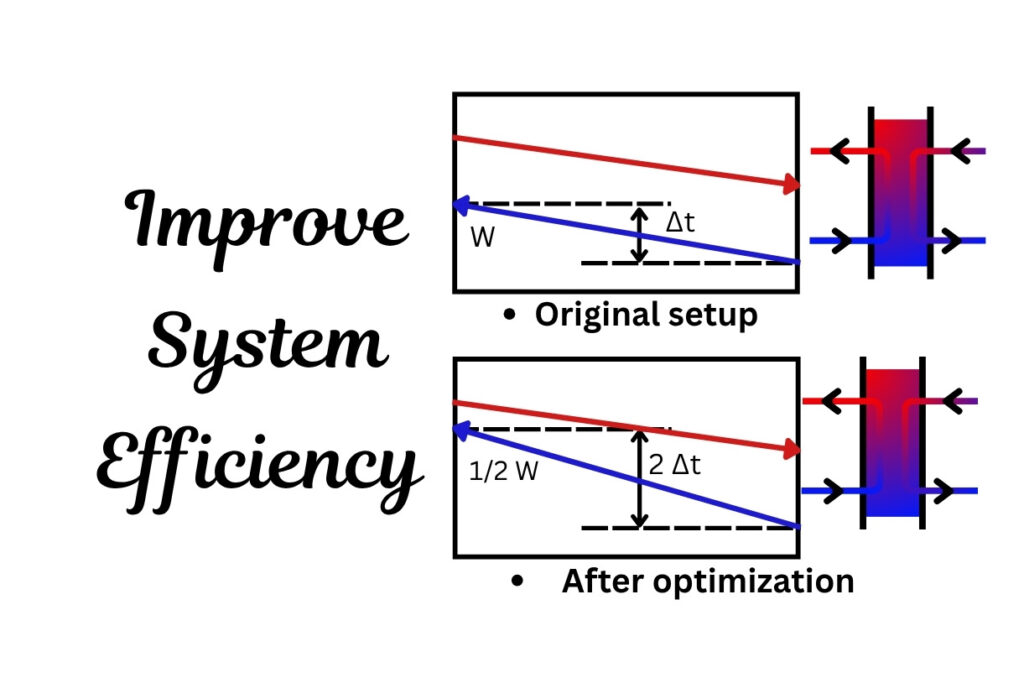
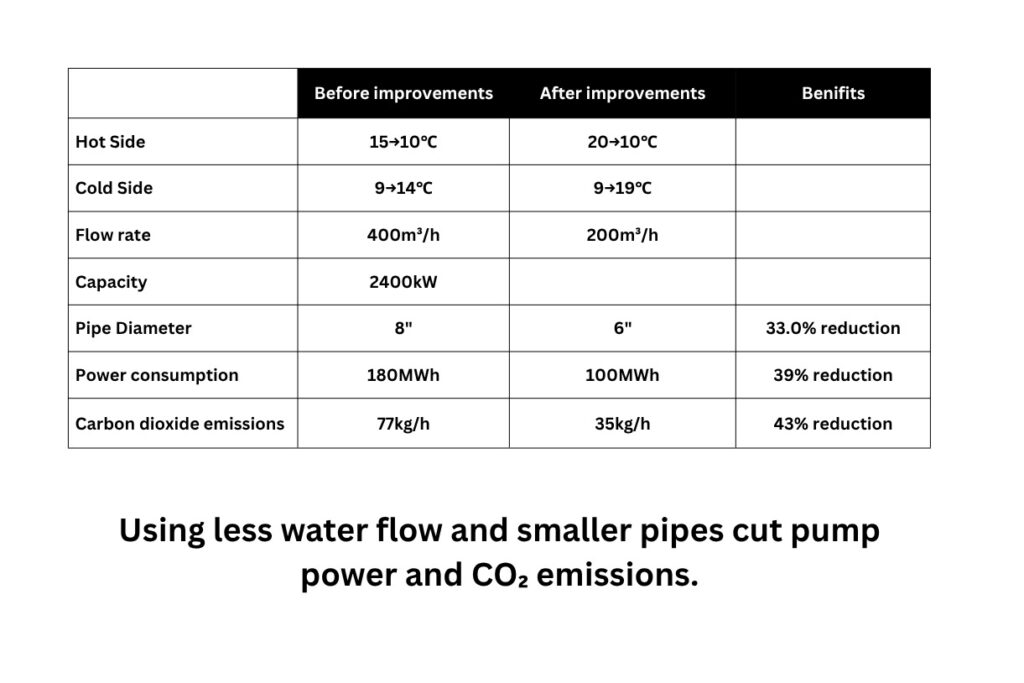
Why is the U-Value So Important for Your Industry?
The U-value isn’t just an abstract number; it has tangible consequences across a wide range of industries. Optimizing this coefficient is key to improving processes, reducing costs, and ensuring product quality.
- HVAC: In heating, ventilation, and air conditioning systems, a heat exchanger with a high U-value can heat or cool a building more effectively, leading to significant reductions in energy consumption and lower utility bills.
- Food & Beverage Production: For processes like pasteurization, sterilization, and wort cooling, precise temperature control is non-negotiable. A high and predictable U-value ensures that products are heated or cooled to exact temperatures, guaranteeing food safety and preserving delicate flavors.
- Power Plants: In power generation, efficiency is paramount. Heat exchangers are used to recover waste heat from exhaust gases or to cool critical systems. A higher U-value means more energy is recaptured, boosting the overall output of the plant.
- Automotive & Manufacturing: From cooling hydraulic fluids and lubricating oils to managing temperatures in chemical processes, industrial heat exchangers keep machinery running smoothly. An efficient unit prevents overheating, reduces downtime, and extends the lifespan of expensive equipment.
- Oil & Gas: In refineries, heat exchangers are used extensively to heat and cool hydrocarbons. A superior U-value allows for better energy integration within the plant, directly improving process yields and operational profitability.
What Factors Influence the U-Value?
The overall heat transfer coefficient isn’t a fixed constant. It’s a dynamic value influenced by several interconnected factors:
- Fluid Properties: The type of fluids being used is fundamental. Viscosity, density, specific heat, and thermal conductivity all play a role. For instance, water transfers heat much more effectively than viscous oils.
- Flow Rate and Turbulence: As the flow rate of the fluids increases, so does the turbulence. In a Gasketed Plate Heat Exchanger (GPHE), the corrugated plates are specifically designed to induce high turbulence even at low flow rates. This turbulence breaks up the thermal boundary layer, dramatically increasing the U-value.
- Material of Construction: The thermal conductivity of the plates themselves is a component of the overall calculation. While materials like copper are highly conductive, the choice is often dictated by the fluid’s corrosive properties. Materials such as 316/304 Stainless Steel, Titanium, C-276 Hastelloy, and 254 SMO offer an excellent balance of thermal performance and corrosion resistance.
- Fouling: This is the arch-nemesis of thermal efficiency. Over time, deposits like scale, sediment, biofilms, or chemical residues can build up on the heat transfer surfaces. This “fouling layer” acts as an insulator, creating a thermal barrier that can drastically reduce the U-value and cripple performance.
How Can You Maximize the U-Value of Your Heat Exchanger?
Ensuring your heat exchanger operates at its peak potential involves a combination of smart design choices and proactive maintenance. As discussed in guides on heat exchanger applications, choosing the right unit and maintaining it properly are crucial.
- Start with the Right Design: The first step is selecting a heat exchanger that is properly sized and configured for your specific duty. Using an online tool can help you input your parameters—like fluid types, temperatures, and flow rates—to find the optimal design. For a detailed analysis, try our Heat Exchanger Calculator.
- Prioritize Regular Maintenance: As fouling is the primary enemy of a high U-value, a consistent cleaning schedule is essential. Whether it’s mechanical cleaning or a clean-in-place (CIP) procedure, removing fouling restores the heat exchanger to its original design efficiency. As we’ve noted in articles about troubleshooting, dealing with performance drops promptly prevents larger issues.
- Use High-Quality Components: The performance of a GPHE is only as good as its parts. Worn-out plates or failing gaskets can lead to internal leaks, pressure drops, and reduced efficiency. When it’s time for a replacement, using high-quality components ensures a proper fit and restores performance. At Heating Formula, we offer a complete range of GPHE Spare Parts to keep your operations running smoothly.
Heating Formula: Your Partner in Thermal Efficiency
At Heating Formula, we understand that achieving a high U-value is central to your success. As a leading heat exchanger manufacturer in Turkey, we specialize in creating thermally efficient solutions for the world’s most demanding industries.
We supply a wide variety of Gasketed Plate Heat Exchangers (GPHEs) and Shell & Tube exchangers designed for maximum performance. Furthermore, we provide a comprehensive inventory of spare parts, including plates made from 316/304 SS, Titanium, C-276 Hastelloy, and 254 SMO, as well as durable EPDM, NBR, and Viton gaskets. Our parts are engineered to be fully compatible with leading OEM brands like Alfa Laval, Sondex, APV SPX, Funke, Schmidt, Vicarb, Gea, and Tranter, offering you a reliable and cost-effective alternative.
Ready to optimize your thermal processes? Explore our GPHE Selection or contact our engineering team today.
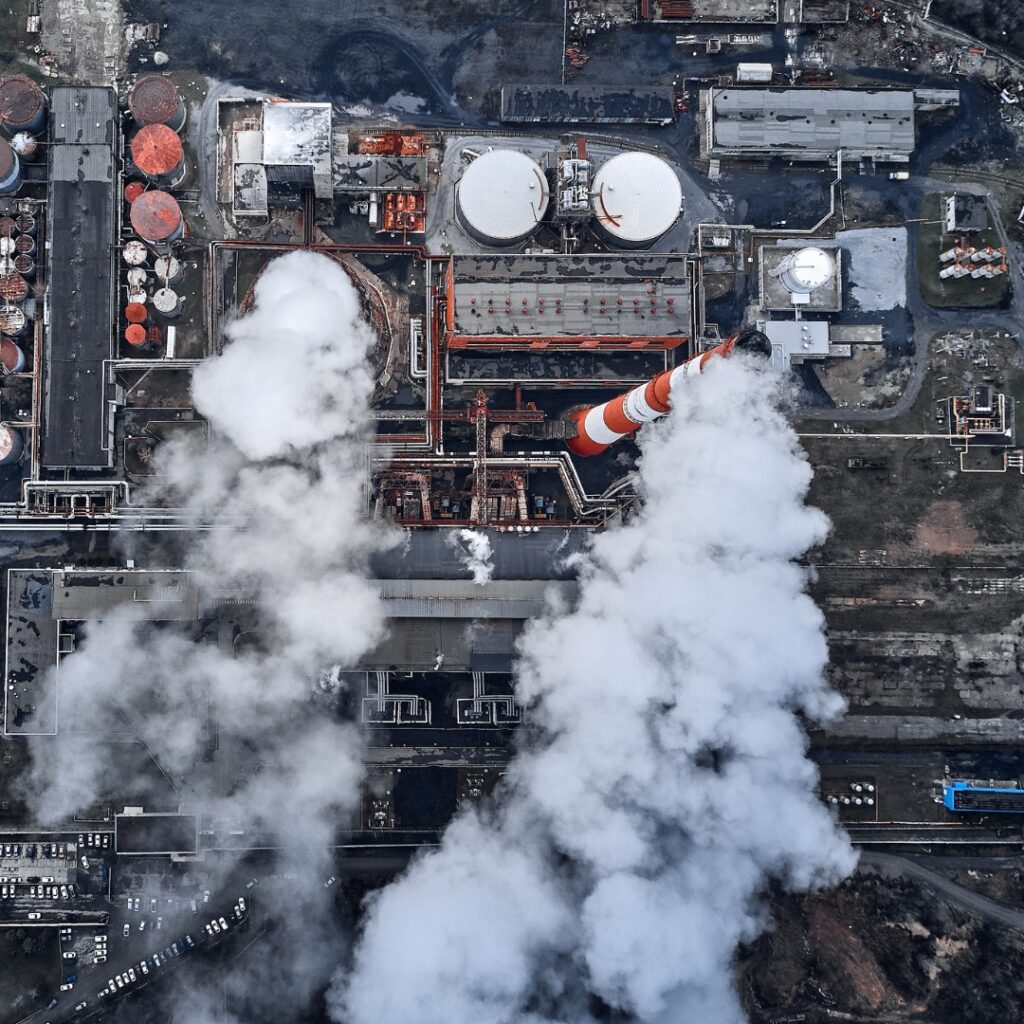
Frequently Asked Questions (FAQ)
Q: What is a good U-value for a heat exchanger?
A: There is no single “good” U-value, as it depends entirely on the application, the fluids involved, and the type of heat exchanger. For example, a water-to-water application in a plate heat exchanger might have a U-value between 800-1500 W/m2K, while an oil-to-oil application might be in the 100-400 range. The goal is to maximize the U-value for your specific conditions.
Q: How does fouling affect the U-value?
A: Fouling adds a layer of material with low thermal conductivity to the heat transfer surfaces. This layer acts as an insulator, increasing the overall thermal resistance and significantly lowering the U-value. This leads to reduced performance, forcing you to either increase pumping power or accept lower efficiency.
Q: Can I improve the U-value of my existing heat exchanger?
A: Yes. The most effective way is through regular and thorough cleaning to remove any fouling. Additionally, ensuring your system is operating at the designed flow rates can help. If parts are worn, replacing them with high-quality spares can restore performance. For a significant improvement, you may need to re-evaluate the design with our Heat Exchanger Calculator.
Q: Which plate material is best for a high U-value?
A: While the plate material’s thermal conductivity is a factor, the primary consideration is its compatibility with the process fluids to prevent corrosion and fouling. Stainless steel provides an excellent balance of good thermal conductivity and durability for many applications. For highly corrosive fluids like seawater or acids, Titanium is often the superior choice despite having slightly lower thermal conductivity.
Q: Why do plate heat exchangers often have higher U-values than shell and tube exchangers?
A: Gasketed Plate Heat Exchangers (GPHEs) use corrugated plates that create a highly turbulent, narrow flow path. This turbulence dramatically enhances the heat transfer coefficient compared to the smoother flow typically found in shell-and-tube units. This often makes GPHEs a more compact and efficient solution for liquid-to-liquid duties. Explore our designs on our GPHE Selection page to see the difference.
Sources
- TYPICAL OVERALL HEAT TRANSFER COEFFICIENTS (U – VALUES), Engineering Page, https://www.engineeringpage.com/technology/thermal/transfer.html
- Heat exchanger applications: types, industries & how they work, Tranter, Hisaka
- Troubleshooting for plate heat exchangers, Alfa Laval