Are Spiral Heat Exchangers Worth the Investment? 5 Long-Term Cost Benefits Explained
If you’ve ever wondered how industries efficiently manage heat transfer in sticky situations—like handling sludge, corrosive fluids, or high-viscosity materials—spiral heat exchangers might be the unsung heroes. First patented in the 1930s, these coiled workhorses were designed to solve problems traditional shell-and-tube or plate heat exchangers couldn’t handle. Over the decades, their unique spiral design has made them a go-to for industries like wastewater treatment, chemical processing, and food production. But are they worth the upfront cost? Let’s break down their long-term value—without the jargon.
What Exactly Are Spiral Heat Exchangers?
Picture two metal plates rolled into concentric spirals, creating alternating channels for hot and cold fluids. This compact, self-cleaning design minimizes fouling (that pesky buildup of gunk) and handles tough materials without breaking a sweat. Unlike gasketed plate models, which require frequent maintenance, or shell-and-tube units that take up acres of space, spiral versions thrive in harsh, space-limited environments.
What Types of Spiral Heat Exchangers Exist?
Not all spirals are created equal. The three main types include:
- Welded Spiral Exchangers: Ideal for high-pressure or corrosive fluids—no gaskets to fail.
- Gasketed Spiral Exchangers: Easier to clean and modify, perfect for industries like dairy processing.
- Hybrid Designs: Combine spiral channels with traditional shell-and-tube frames for tricky applications.
At Heating Formula, we specialize in gasketed plate heat exchangers (GPHE), but even we admit spirals outshine them in scenarios involving heavy particulates or extreme temperatures.
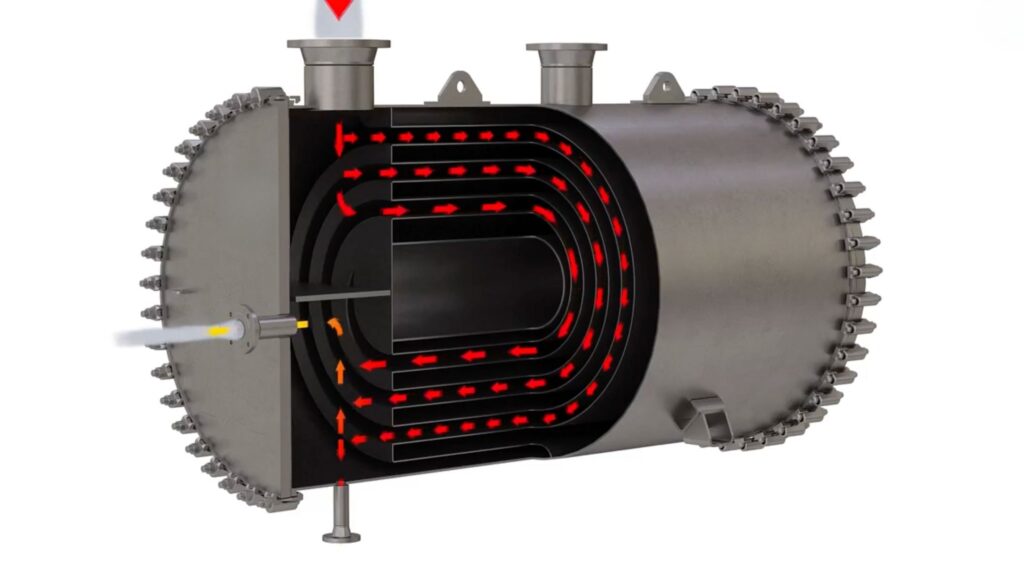
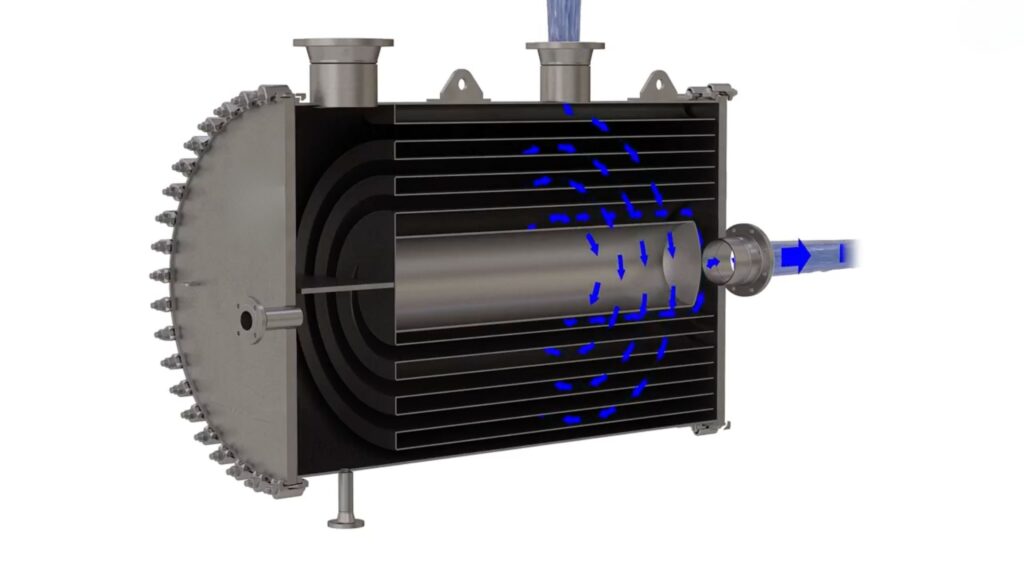
How Do You Choose the Right Spiral Heat Exchanger?
Picking the wrong heat exchanger is like wearing snow boots to the beach—it’ll work, but you’ll regret it. Ask yourself:
- What’s Your Fluid Type? Sludge or abrasive fluids demand welded spirals. For cleaner media, gasketed models save time during maintenance.
- How Much Space Do You Have? Spiral units are compact, but hybrid designs offer flexibility for retrofitting older systems.
- What’s Your Budget? Initial costs are higher, but factor in downtime savings. One paper mill we worked with cut maintenance costs by 40% after switching.
Need help weighing options? Our GPHE selection guide offers tips that apply to spiral models too.
Why Are Spiral Heat Exchangers a Long-Term Money Saver?
Let’s get to the heart of it: five reasons these spirals pay off over time.
1. Do They Really Reduce Maintenance Costs?
Absolutely. The self-scouring spiral channels prevent buildup, meaning fewer shutdowns for cleaning. A wastewater plant in Ohio reported going from monthly cleanings to just once a year. Less downtime = more production hours. Plus, if you ever need parts, reliable suppliers like Heating Formula stock spare parts for GPHEs that share components with some spiral models.
2. Can They Handle the Nastiest Fluids?
Ever tried pumping molasses through a standard plate exchanger? It’s a mess. Spiral designs handle high-viscosity fluids and particulates without clogging. One chocolate manufacturer doubled their output because the spirals didn’t choke on cocoa nibs.
3. How Do They Cut Energy Bills?
Their counter-current flow design maximizes temperature exchange efficiency. Think of it as a highway where hot and cold fluids move in opposite directions, squeezing every bit of heat transfer. Users often see 15-25% lower energy use compared to shell-and-tube units.
4. What’s Their Lifespan Compared to Other Exchangers?
With fewer stress points and corrosion-resistant materials, spiral exchangers often last 20+ years. A chemical plant in Germany still runs units installed in the ’90s—just replace the gaskets occasionally.
5. Are They Worth the Higher Initial Cost?
Let’s crunch numbers. A spiral unit might cost 30% more upfront than a gasketed plate model. But if it saves $12,000/year in maintenance and energy, you break even in 2-3 years. After that, it’s pure savings.
When Should You Stick with Traditional Exchangers?
Spiral models aren’t universal. For simple, low-fouling tasks, our GPHE units or shell-and-tube exchangers offer cost-effective solutions. Always match the tool to the job.
Final Verdict: Are Spiral Heat Exchangers Worth It?
If your operation deals with tough fluids, tight spaces, or sky-high downtime costs, spiral heat exchangers are a smart long-term play. Yes, they cost more upfront, but the ROI in efficiency and reliability is hard to beat. And if you’re ever unsure, Heating Formula’s team can help you compare options—whether it’s spiral, GPHE, or shell-and-tube.
Note from Heating Formula: While we champion spiral exchangers for the right applications, we also supply top-tier gasketed plate heat exchangers and durable shell-and-tube models. Check our inventory for spare parts and expert advice tailored to your needs.